油断している間にまたしてもインターバルが空いてしまいました。このままでは今月の投稿がゼロになってしまう……! と慌てての更新です。
製作中のファイヤーバードはひとまず置いておいて、今回はギターの『塗装剥がし』をやってみましょう。
ジャンクパーツを使ってギターを工作する場合、もちろん購入時の塗装を活かすのもアリですが、やっぱり工作好きとしては自分の好きな色で仕上げたいですよね。ジャンク工作をするうえで『塗装剥がし』は必須科目といえるかもしれません。
今回塗装を剥がすのは、リサイクルショップで買ったレスポールタイプのボディ。メーカーは不明です。
ムラサキ色がかっちょいレスポールです。ネックはボルトオンタイプ。なんか指紋がきたなくてすみません……。
以前、レスポールキット製作時の塗装の回にも書きましたが、ギターの塗装仕上げには大きく『ウレタン仕上げ』と『ラッカー仕上げ』というものがあります。一部を除き市販の製品のギターのほとんどが『ウレタン仕上げ』で、今回のレスポールボディも『ウレタン仕上げ』のようです。
ウレタンの特徴は何と言っても塗膜が頑丈な事です。試しに電動サンダーを使ってヤスってみましたが、トップ面を剥がすのだけで四苦八苦……。ボディ全体を全部剥がすとなると一体何時間かかるかわかりません。さすがウレタン塗装、丈夫で頼もしい! ……と言いたい所ですが、工作して弄りたい者としてはなかなかの強敵というわけです。
しかし世の中には、筆者のように根気や体力が乏しい人間にとってとても便利な道具がありました……! その名も『ヒートガン』!
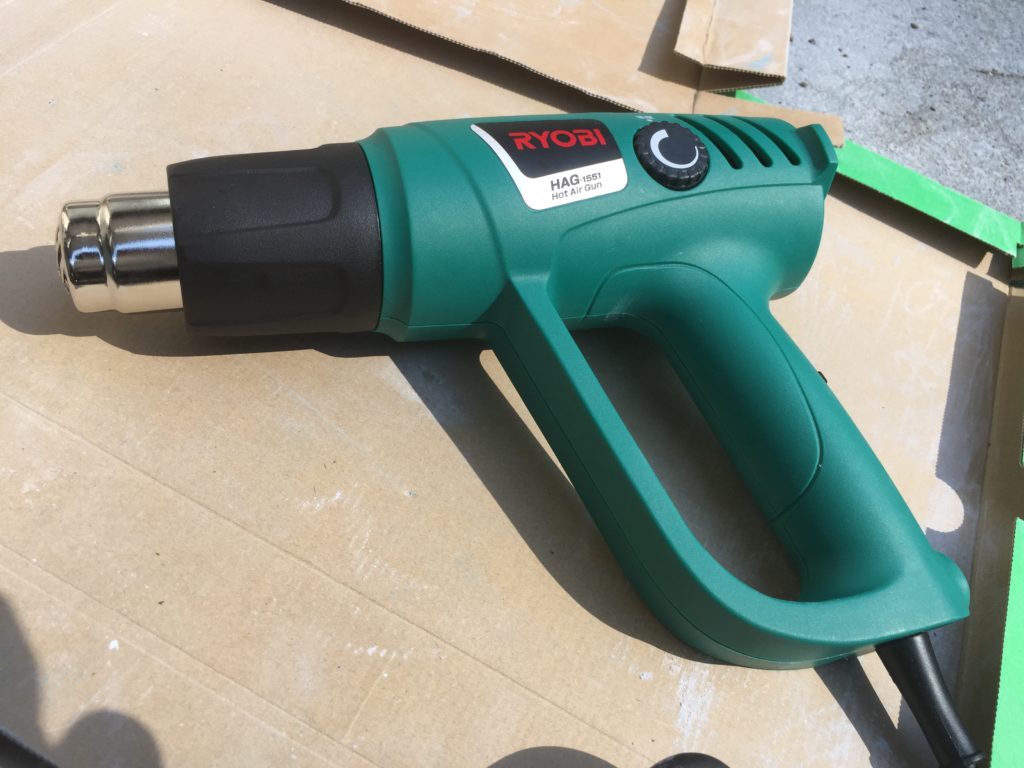
ヒートガン! 何かの武器みたいでかっこいいですね。これは熱風を吹き出す道具で、『ドライヤーの凶暴なやつ』とでも申しましょうか。
このヒートガンから出る熱風をブワ〜! っと当てて塗装面がやわらかくなってから、スクレーバーでガリガリこそげてやると、とても簡単に塗装を剥がすことができました。これが実に楽しい作業で、ベロベロベロ〜! と一気に塗装が剥がれてゆくのはなかなか快感だったりします。
頑張ってサンダーで剥がしたトップ面にも、まだまだ塗装が残っています。サイドもがんばろうとしたのですが、ギブアップ……。
ヒートガンを使えばあっという間。それまでの苦労がウソのようです。
始めのうちは、どのくらいヒートガンを当てればいいのかわからず、ちょっと焦がしてしまったりもしたのですが、コツは掴むまでにそんなに時間はかかりませんでした。(多少焦げてしまってもヤスリで削ればすぐ直りますが、火傷には十分注意しましょう!)
ついでに、同じくジャンクのネックも剥がしてみましょう。こちらは、当ブログでは度々登場の、おなじみフォトジェニックです。
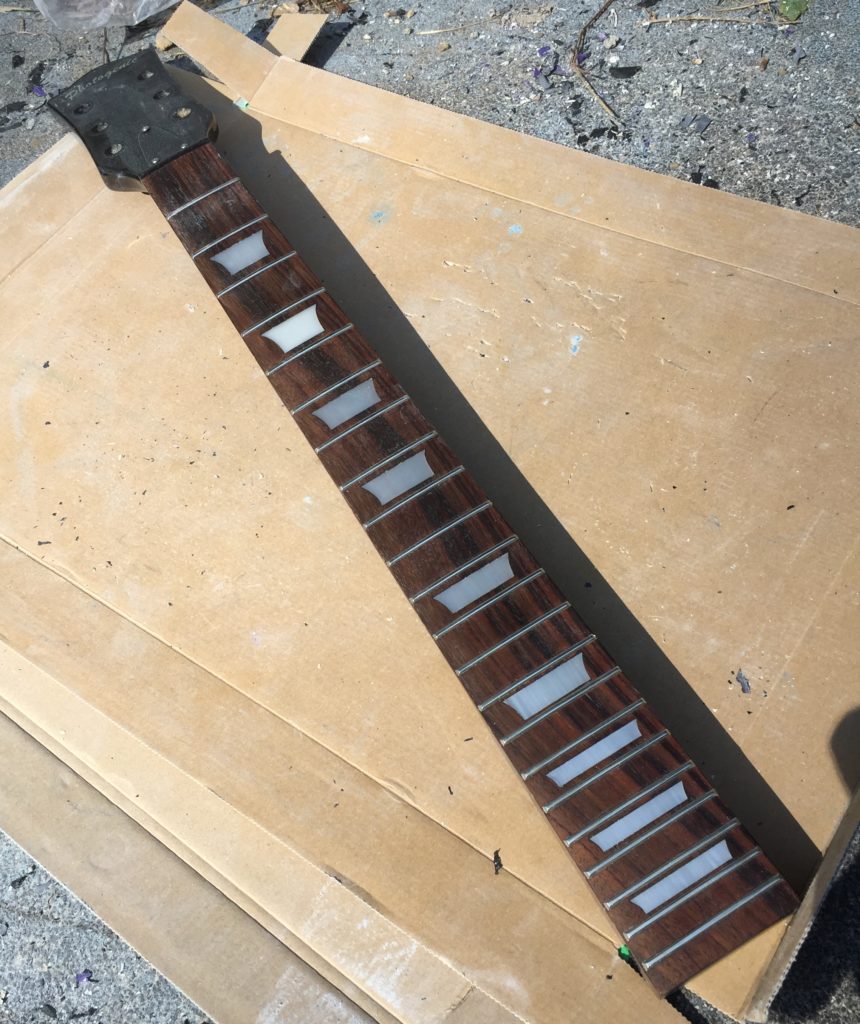
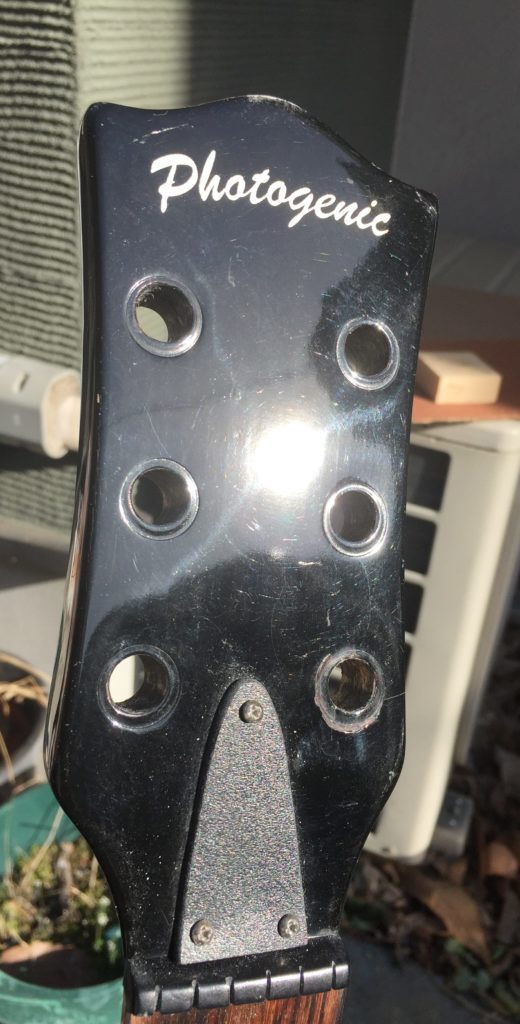
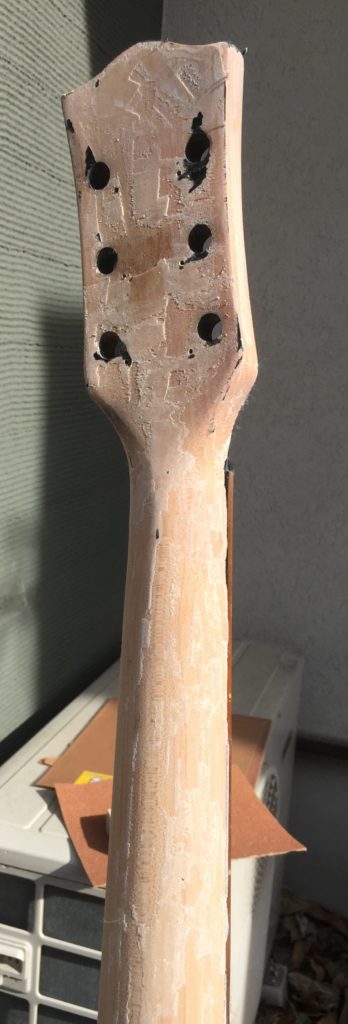
やはり木の色が出てくると、工作意欲がググッと高まりますね! さてさて、こいつはどんな色にしましょうかね?